This is one of the questions Bottom Paint Store is asked the most.
Let’s start with explaining that gelcoat is not a paint but a type of resin that is used to provide a protective layer over fiberglass.
Key takeaways on how to apply gelcoat:
- Clean the repair area and all tools with acetone prior to application.
- Do not work in direct sunlight. Choose a shady location or an overcast day.
- Catalyze your material so that it has a longer pot life.
- Apply the gelcoat using a brush or spray gun.
- Apply gelcoat in 4-5 layers at approximately 5 mils each, allowing 15-20 minutes between layers for a total thickness of 20-25 mils.
- Use a gelcoat thickness gauge to ensure proper thickness is achieved.
- Once gel coat has tacked up, about 20 minutes after final layer has been applied, lay-up of the part can begin.
Here are the steps to apply gelcoat using a brush.
Below you will find a detailed gel coat preparation guide on how to apply gelcoat to your boat, RV, or other surfaces. The secret to a good finish is to apply the gelcoat properly. The application of gelcoat is pretty straightforward when you follow this guide.
Determine the Existing Surface: First thing you want to do is look at the surface on which you want gelcoat applied. If the surface is already coated with gelcoat, or if the surface is a fiberglass or polyester resin, then the application of gelcoat is a snap. If the surface is painted then the paint should be removed before the gelcoat is applied.
We offer pre-mixed colors of gelcoat, use this color chart as a guide for the available colors that we have.
Prepping the Surface: Remove rails, cleats, louvers, snaps, striping tape, etc. Duct tape off adjacent gunwale molding, and deck fittings you are unable to remove. **NOTE** Duct tape is recommended over masking tape because it provides better protection. Remove seals from the edges of parts or fittings when doing a repair around that part or fitting. Take steps to cover and protect the rest of the boat before starting. When working on the deck or cabin, tarp off the adjacent areas. 3M and UV tapes , and masking papers are recommended.
Sanding Existing Gel Coat: You want to sand the surface to make a mechanical bond to the gel coat. Our technicians suggest the use of Dyekum Steel Blue Dye to be really thorough. Steel Blue is a dye you’re going to wipe on or you can use the blue dye spray. If you don’t see the blue dye again, you know you’ve sanded it all properly. Start by sanding the surface with 150 grit or sandpaper. The heavier fast-cut grits (40/80/100) are used to feather sand and ground out a routed area prior to filling. Also, they are used for the first sanding of gouges, dock dings, scratches, and blisters. When sanding areas that have been filled with putty we suggest using 40 or 80 grit sandpaper, depending on how large the repair is. Once the fill area is level or contoured to the desired shape, sand with 100 grit paper to remove the course scratches from 40 or 80 grit. You should also feather the surrounding area of the gel coat repair with 220/330. At this point, the repair is ready to prep and spray/brush with gelcoat. Use 3M Abrasives for best results.
Preparing the Surface for Application: Next, you’re going to have to clean the surface. We encourage the use of Acetone, because it does not leave residue and evaporates easily. When the surface is clean, you want to get moving fairly quickly; if the surface is sitting for some amount of time, you want to re-clean the surface. Dust and dirt particles are your enemy here, so make sure you clean the surface thoroughly.
Determine whether you need one or two gelcoat coats. If you change colors, it will require at least two gelcoat coats.
If this is going over a patch, at least 2 coats are recommended to get a uniform surface. Otherwise, there will be only one coat.
Method of Application: Next, determine if you are going to brush, roll or spray your gelcoat so you can prepare the gelcoat for application. If you have Professional Grade Exterior Gelcoat you may either brush/roll or spray. When rolling on gelcoat be sure to use a 1/8 “or 1⁄4” solvent-resistant nap. Be sure not to use foam rollers because they tend to leave the bubbles. If you brush on the gel coat, make sure to use a solvent resistant brush.
Gel Coat Additives: You should also determine which additives you will use with your gelcoat application.
- Wax Additive: Add up to 4 oz of Wax Additive per gallon 1 oz per quart for tack-free surface on the final coat, or if applying one coat a recommended film thickness. The Exterior Gelcoats that recommend a wax additive is included with purchase at Bottom Paint Store. (A wax additive is NOT used with Brushable Gel Coat or HI UV Clear.) You should only use a wax additive in the final application coat or if you are planning on only one coat.
- Partall Film #10 PVA Surfacing Agent For Gel Coat: Use this product as a surfacing agent when using Gel Coat without wax additive and typically larger spray applications. Partall Film #10 is a polyvinyl alcohol (PVA) water/alcohol solution of water-soluble, film-forming materials. This parting film is particularly recommended as a parting agent for separation between polyester or epoxy resins and various mold surfaces. It is not recommended for use with resins containing water or giving off water during cure (i.e., phenolics) or with automotive finishes, as damage may occur. Partall Film #10 will not shrink and pull away from corners or curved surfaces. After the resin has dried, the film parts easily from the mold and is readily dissolved from the molded parts with water. An occasional coating of Partall Paste #2 is required on most mold surfaces before application of Partall Film #10. May be applied over gelcoat as a surface cure agent. (recommended for HI UV Clear since no wax should be added)
- Patch Booster Gelcoat Additive is an additive that significantly improves the application, appearance, and longevity of gelcoat patches. Patch Booster eliminates the need to thin, side-promote, or add wax to gelcoat prior to patching. Formulation enhancements have lengthened the shelf life of a sealed can to (1) year while maintaining a sand-able cure in 1-3 hours. Do not use any other wax additive when using Patch Booster. Patch Booster should be used with Professional Grade Exterior Gel Coat. Another popular additive option is the Duratec Hi-Gloss Additive Clear, see the tech data sheet for mixing details for all items.
- Tinting: Neutral Gelcoat may be tinted using Pigments for Gel Coats and Resins which are designed for use in Neutral gel coats. Do not use more than 1 oz tint per quart.
Catalyzing Gelcoat with MEKP: All gelcoat MUST be catalyzed with MEKP to cure. This should be added after all other additives just prior to application. Gelcoat requires Methyl Ethyl Ketone Peroxide or MEKP to enable the process of hardening. It’s a very small number. We suggest 1-1/4% to 1-1/2% by volume, i.e. 13-15 cc per quart. Darker colors need a little more catalyst for the same reaction, so you can catalyze up to 2%. All Gel Coats from Bottom Paint Store come with MEKP with each gelcoat purchase. Refer to the catalyst chart located on the product page for the gelcoat you are using or follow the label guidelines. As a general rule: The catalyst level (MEKP) should not exceed 3.0% or fall below 1.2 for proper cure. Ideal range is 1.8% @ 77°F. Gel time at 1.8% MEKP is 10-17 minutes. This time element is dependent on material temperature, room temperature, humidity, air movement, and catalyst concentration.
Gelcoat should not be used when temperature conditions are below 60°F, as curing may be adversely affected. Be sure to have a good strategy when applying your gelcoat. Once you mix and catalyze, you have about 15 minutes to apply the gelcoat before it starts getting hard or starts to “gel.” The actual working time depends on the amount of catalyst and how hot the working conditions are. Anything below 60 degrees, and your gelcoat will not cure, but as you get warmer and warmer, your working time will decrease rapidly. At 70 degrees, you get 15 minutes, but at 90 degrees, you only get 5 minutes. If you need more time to work, be sure to sit the can in some cold ice water to cool it down to 60 degrees to allow you a little more working time.
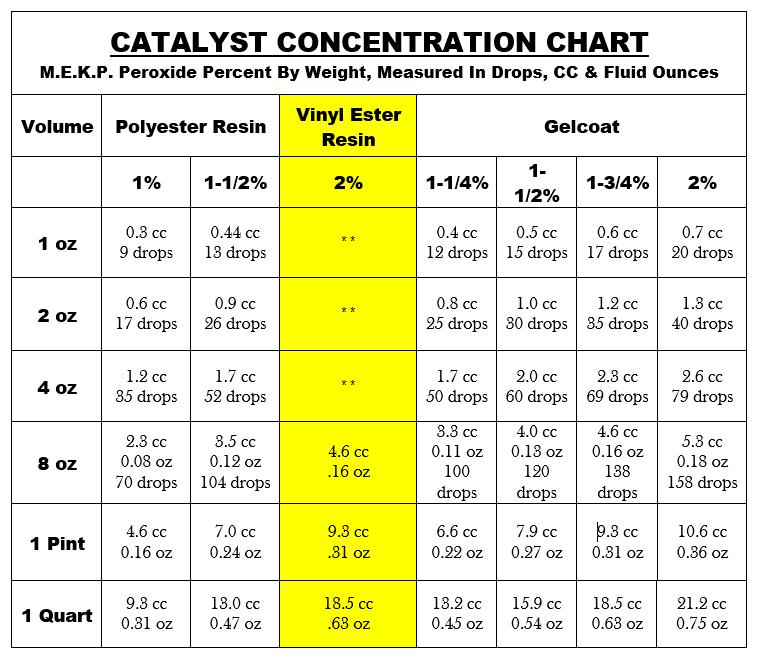
The weight of MEKP 925 is 1.125 grams per cc. 30 drops is approximately equal to one cc.
cc = cubic centimeter. Oz = fluid ounce
Note: Using drops for catalyst measurement is only an estimate. In critical applications MEKP should be measured using cc’s or fluid oz’s which are volume measurements.
The percentages in the chart: 1% thru 2%, are percentages of resin or gelcoat by weight. The cc and oz values in the chart have been converted from weights of MEKP to volumes of MEKP.
- 1 ML = 1 CC
- If using a wood mixing stick, place the stick in resin before adding catalyst so the wood doesn’t absorb catalyst
- Only catalyze slightly more than needed. Resin that cures still in the mixing pot is unusable. Mix small batches at a time since too much MEKP will result in the hardening of the gelcoat way too fast! Refer to the catalyst chart located on the product page for the gelcoat you are using or follow the label guidelines.
- Gel Coat requires the addition of fiberglass resin hardener or catalyst (MEKP) at 1.8% by volume (77ºF) (approximately 12 drops per ounce)
- Measure catalyst accurately. Under or over catalyzation retards curing and causes fading and chalking
- All Gelcoats from the Bottom Paint Store comes with the MEKP catalyst but additional amounts can be purchased.
Applying Gelcoat by Brush or Roller: Choose a good pure (natural) resin-resistant bristle brush with tapered ends. Avoid brushes that are either too stiff or too soft. For most work, a 3″ or 4″ wide brush will suffice. If there is a trim color, you should have a narrow trim brush on hand. Our Gelcoat comes with MEKP hardener with every purchase, but you may need more which you can purchase as an option depending on the application, temperature, and other environmental factors. Please refer the to Catalyzation chart on the Gelcoat page or on the label. Gelcoat needs to be applied evenly. We suggest a thickness of 18-20 mils to properly cure. The thickness of the matchbook cover is approximately 18 mil. If you’re not sure how thick it is, pick up a mil gauge. This is a simple, easy way to see the thickness of your gelcoat. See this article for more information: How to Apply Gelcoat by Brush and Roller.
Spraying Gelcoat: For best results spraying gelcoat, it is recommended to use a spray gun designed specifically for applying gelcoat and resins, such as the professional grade spray guns offered by FGCI and ES Manufacturing.
Next decide if you want to use an aluminum, plastic or paper cup to house the gelcoat. You can use either a heavy-duty, reusable plastic cup or disposable paper cup for spraying gelcoat. There are also disposable cup liners available that you can insert into the plastic Poly-Pro graduated cup or paper cup. You can mix your material right in the lined cup and then simply insert the cast aluminum lid onto the lined cup, attach the cup to the gun and you are ready to spray.
Can I spray gelcoat with an airless sprayer? Yes, you can spray gelcoat with an airless sprayer however it is it is recommended to use a pressure of 3000 psi.
The pressure at which you spray gelcoat depends on the type of gun you are using. For example, if you are using a conventional spray gun, you should set the pressure between 30 and 50 psi.
Please follow the instructions located on the products page or the label. Spraying Gelcoat delivery rate of no more than 2.5 pounds per minute with conventional air atomized spray, and no more than 4 pounds per minute with airless equipment. Spray: Airless or Conventional: 2.0-2.5 orifice tip. Use a gelcoat spray gun such as ES Manufacturing Gelcoat Spray Gun G830, ES-G100 Spray Gun, or equivalent.
You will need to thin the gelcoat for it to run through the spray gun. There are 2 thinners that are recommended by the manufacturer when spraying gelcoat: Patch Booster, and Duratec. Patch booster is used with a 5:1 ratio or about 20% by volume. Do not use any other wax additive when using Patch Booster. Duratec is for a cosmetic high gloss finish. It has to be mixed at a 1:1 ratio with gelcoat. Since manufacturer specs change often due to formula updates be sure to follow the most recent recommendations from the technical data sheets. Some customers use Styrene for thinning but the manufacturer warns it can affect the gelcoat colors although this is the most cost-effective option and doesn’t have the added wax.
Initially spray a cover coat as smooth and evenly as you can to cover your repair. This coat should be mostly in the repair area and may be repeated. Sanding between coats is not necessary unless a surfacing agent has been added to your gel coat. Once your repair is covered, feather a ‘flow’ or sanding coat on the masked-off area making layered passes to avoid a buildup of gel coat in any one area. Each of these coats of gelcoat may involve several passes. Be even and consistent in your gun movement, overlapping each previous pass slightly and not hesitating on the ends. When spraying to a radius, flow the gelcoat to the tape. In open flat areas, layer passes. The final thickness should be 16-20 mils minimum or the gelcoat may not fully cure. Gelcoat needs to be applied evenly. We suggest a thickness of 18-20 mils to properly cure. The thickness of the matchbook cover is approximately 18 mils. If you’re not sure how thick it is, pick up a mil gauge. This is a simple, easy way to see the thickness of your gelcoat. As soon as you are done spraying, clean your sprayer fully with acetone. Most re-sprayed gelcoat will cure in 2-4 hours, although overnight cures are ideal.
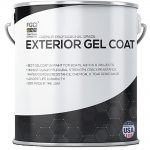
Finishing your Gelcoat Application: If you’re using our Professional Grade Exterior Gelcoat, you’ll be ready to sand and buff your freshly gelcoated surface once it has cured to a hard surface. You should not be able to dent it with your fingernail. Begin wet sanding with the finest grit that will remove orange peel in the re-sprayed area. This will avoid unnecessary sanding scratches. Usually 320 or 400 grit wet paper is sufficient for the initial sanding. Going up to 400, then 600, and eventually 800 grit sandpaper. Compound and polish with Aquabuff 2000 then happy a wax such as Collinite 925 UV for protection.
Another option is you can use an 800 grit compound for the gelcoat at this stage. You want to use a buffer that turns 1600-3000 RPM. The car polishers won’t work if they’re spinning too slowly, so you want to check the speed of the spin. It’s best to do a 4-foot by 4-foot area at a time. Every 10 feet or so, you’re going to want to clean your pad with a spur or some air to make sure the contaminants don’t scratch your surface.
If you want a perfect, glossy shine, use a machine glaze and then two wax coats,
and you’ll have a stunning, glossy professional finish.
IMPORTANT GELCOAT APPLICATION TIPS:
DO NOT WORK IN DIRECT SUNLIGHT -Choose a shady location or an overcast day. You should catalyze your material so that it cures as quickly as possible within your working time. Generally, mix one-pint batches. A good practice is to pour the mixed gel coat from the mixing container into another container used for application. This further assures that no uncatalyzed material is clinging to the sides of the pot. “Lay on” the gel coat in a heavy thickness (about 10 mils) using horizontal strokes, and working from top to bottom. Avoid re-brushing as this could remove the waxy surface additive. Remember to always lap wet. Generally, one heavy coat is sufficient. However, if you have opacity problems two coats may be necessary with a light sanding between coats. Once the coating (gelcoat) has cured, it should be block sanded using 250 wet grit paper to remove all brush marks and high spots. Following this, it should be wet sanded with 320, 400, and 600 wet grit paper, buffed, polished and waxed.
- Clean repair area and all tools with acetone prior to application
- Pot life (amount of time for application of the product) shortens dramatically as you mix larger batch sizes. Keep in mind that you have a limited time to apply what you have mixed (usually between 5-15 minutes).
- Measure catalyst accurately. Under- or over-catalyzed gel coat will cure slower and look faded or chalky.
- Use the recommended thinners/additives only which are listed on the gelcoat’s product page.
- Gel coat will not fully cure without adding a surfacing agent or over spraying with PVA
- Check color thoroughly before applying. Gelcoat will not darken or change colors when it dries. The color wet is the color when dry.
- Store gel coat in a cool, dry place
- Gelcoat should be applied at temperatures of 60ºF to 80ºF
- Always use eye and hand protection
- Gelcoat should not be applied over paint, wood, metal, or concrete. It usually will not adhere to these surfaces.
- Gelcoat will not fully cure without adding a surfacing agent or wax additive sanding aid. You can over-spray with PVA before gel coal reaches its gel stage (5-10 min.), or add 1oz per quart/ 4 oz per gallon of wax additive sanding aid.
- Read all warnings on product labels and only use additives recommended as described per each product.