Professional Grade Exterior Gelcoat can be applied either by Spraying, Brushing or Rolling. This article will discuss how to apply the gelcoat with the brush and roller method. For a more comprehensive guide on How to Apply Gelcoat, please read this article. We will assume you have already read the article to learn about prepping the surface, sanding, and finishing the gelcoat.
Catalyzing Gelcoat with MEKP
All gelcoats MUST be catalyzed with MEKP to cure. This should be added after all other additives just prior to application. We suggest 1-1/4% to 1-1/2% by volume, i.e. 13-15 cc per quart. We do NOT recommend mixing more than 1 quart at a time. Darker colors need a little more catalyst for the same reaction, so you can catalyze those up to 2%. All Gelcoats purchased from the Bottom Paint Store come with MEKP. Refer to the catalyst chart located on the product page, the product label, or the one below.
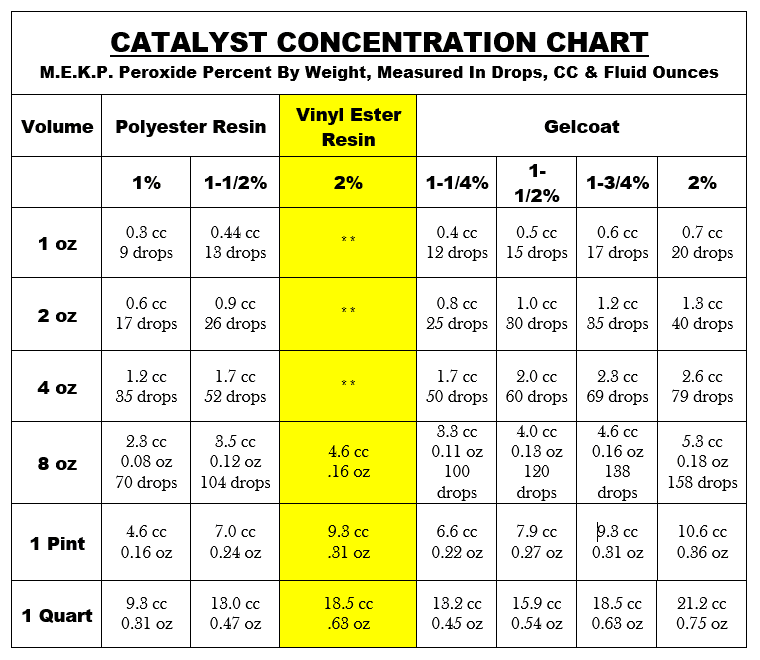
The weight of MEKP 925 is 1.125 grams per cc. 30 drops is approximately equal to one cc.
cc = cubic centimeter. Oz = fluid ounce
Note: Using drops for catalyst measurement is only an estimate. In critical applications MEKP should be measured using cc’s or fluid oz’s which are volume measurements.
The percentages in the chart: 1% thru 2%, are percentages of resin or gelcoat by weight. The cc and oz values in the chart have been converted from weights of MEKP to volumes of MEKP.
NOTE: The catalyst level (MEKP) should not exceed 3.0% or fall below 1.2 for proper cure. Ideal range is 1.8% @ 77°F. Gel time at 1.8% MEKP is 10-17 minutes. This time element is dependent on material temperature, room temperature, humidity, air movement, and catalyst concentration. Gelcoat should not be used when temperature conditions are below 60°F, as curing may be adversely affected.
Be sure to have a good strategy when applying your gelcoat. Once you mix and catalyze, you have about 15 minutes to apply the gelcoat before it starts getting hard or starts to “gel.” The actual working time depends on the amount of catalyst and how hot the working conditions are. Anything below 60 degrees, and your gelcoat will not cure, but as you get warmer and warmer, your working time will decrease rapidly. At 70 degrees, you get 15 minutes, but at 90 degrees, you only get 5 minutes.
TIP: If you need more time to work, sit the can in some cold ice water to cool it down to 60 degrees to allow a little more working time.
Application
Brushing: Use a solvent resistant brush. The chemicals in the gelcoat can be harsh on materials not designed to withstand them. Using a solvent resistant brush should stop any brush materials from getting in the finished product.
TIP: Choose a natural bristle brush with tapered bristles that are not too stiff.
Apply gelcoat quickly using long brush strokes to help achieve an even thickness and to help remove trapped air pockets. Load the brush fully with gelcoat each time. Applying the gelcoat quickly will help you apply it to the correct thickness. Gelcoat applied too thin will not cure properly. Remember, this gelcoat has been catalyzed and the clock is ticking. Also, large amounts of gelcoat left in the container allows a buildup of exotherm and causes the gelcoat to cure too quickly. Once all the gelcoat is out of container and on the surface then you can spend time tidying up with the brush strokes.
TIP: Try to finish vertical areas with an upward brush stroke. This will help reduce sag.
Rolling: Use a solvent resistant 1/8 or 1/4 inch nap roller. Be sure not to use foam rollers; they tend to leave bubbles. Wrap the roller in painters’ tape and rip the tape off to remove loose fibers from the roller. Apply the gelcoat to the surface quickly. Remember, this gelcoat has been catalyzed and the clock is ticking. After wetting out a small area with the roller, use the tip of a brush to smooth out the stipple left by the roller. Move the brush in smooth strokes perpendicular to the direction that the roller moved. Be careful to not apply too much pressure during this step. Ask a friend to assist with the tipping to speed things along. When rolling or brushing on the second coat be sure to apply in the opposite direction from the previous coat. This allows for a uniform finish.
Overview
The 1st coat will consist of gelcoat and hardener only. Wait a half hour for the gelcoat to set. It should be tacky. It will not be fully cured yet.
The 2nd coat will consist of gelcoat, hardener, and wax additive sanding aid. 1 oz of sanding aid per quart or 4 oz per gallon. Sanding aid seals the surface from oxygen, causing the surface to dry tack free.
A wax additive is NOT used with HI UV Clear. You should only use a wax additive in the final application coat or if you are planning on applying only one coat.
If you followed all the steps correctly you should have a beautiful application of gelcoat! If you’re using our Professional Grade Exterior Gelcoat, you’ll be ready to sand and buff your freshly gelcoated surface after about 1- 3 hours.